und Mischen
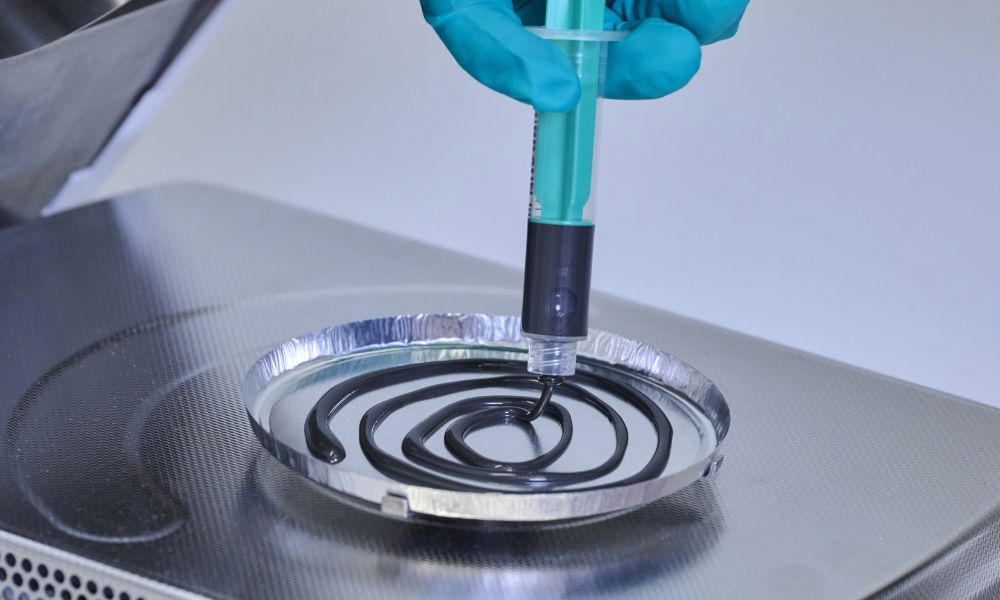
Start der Zellfertigung ist die Produktion der Elektroden. Dafür werden unterschiedliche Aktivmaterialien in einem bestimmten Verhältnis mit Bindern und Lösemitteln kombiniert. Das sogenannte Slurry entsteht.
und Trocknen
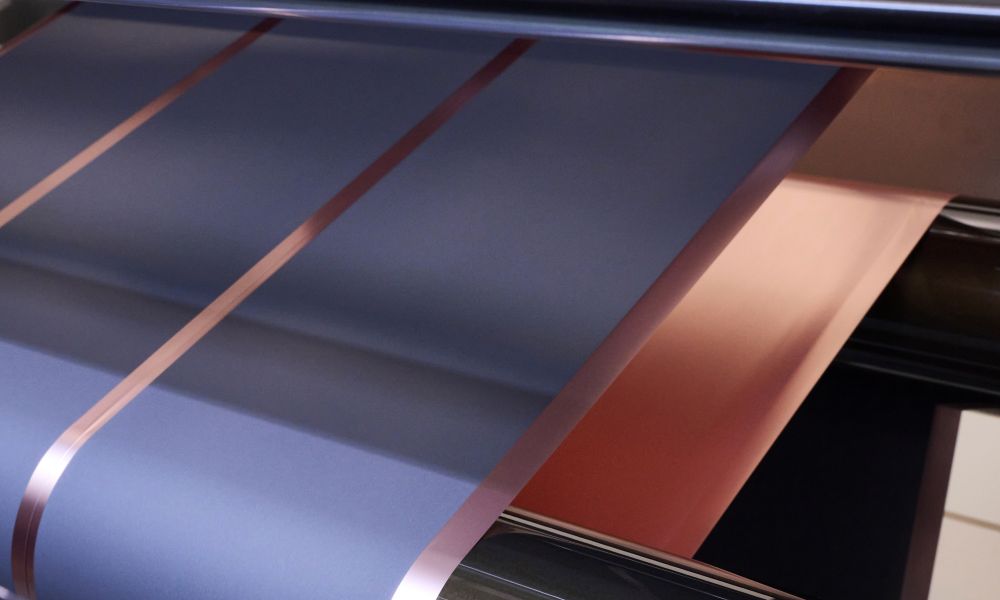
Das Slurry wird auf hauchdünne Metallfolien aufgetragen. Anschließend trocknet die Beschichtung auf einer Strecke von 25 Metern.
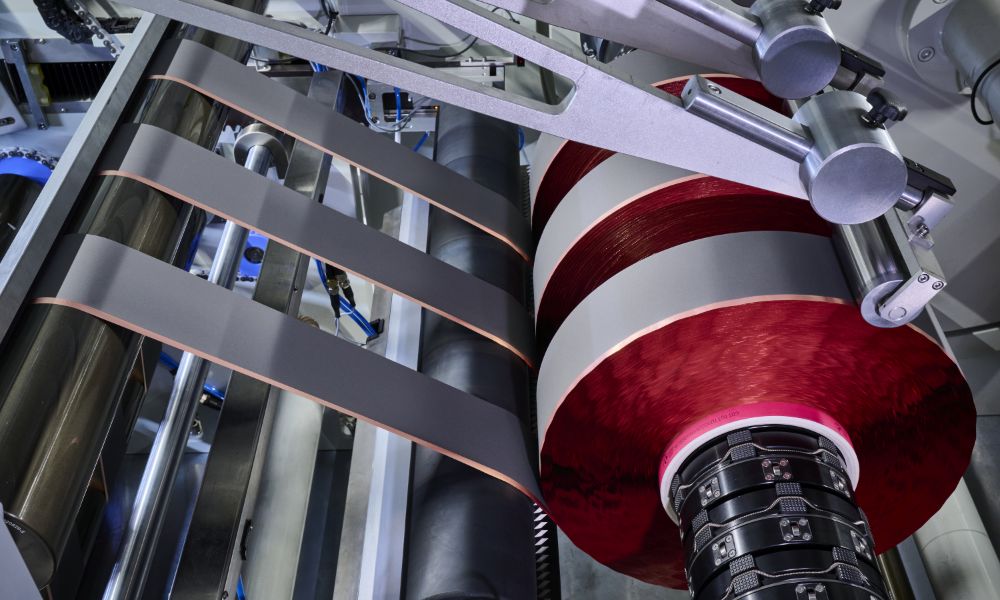
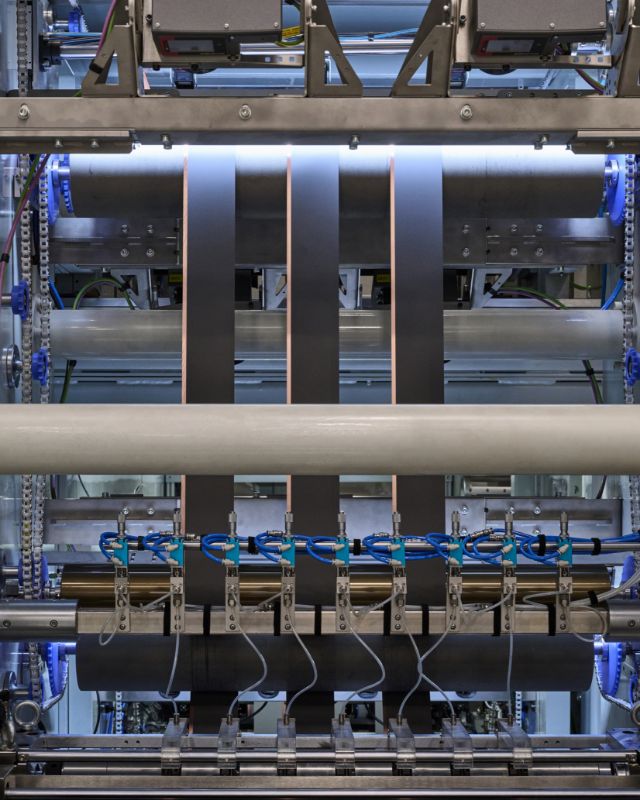
Mehrere Walzenpaare, die sogenannten Kalander, verdichten die beschichteten Folien. Dabei geht es um höchste Präzision: Die Folie ist nur wenige Mikrometer dick, also dünner als die Fäden eines Spinnennetzes. Auch die Beschichtung bewegt sich im Mikrometerbereich.
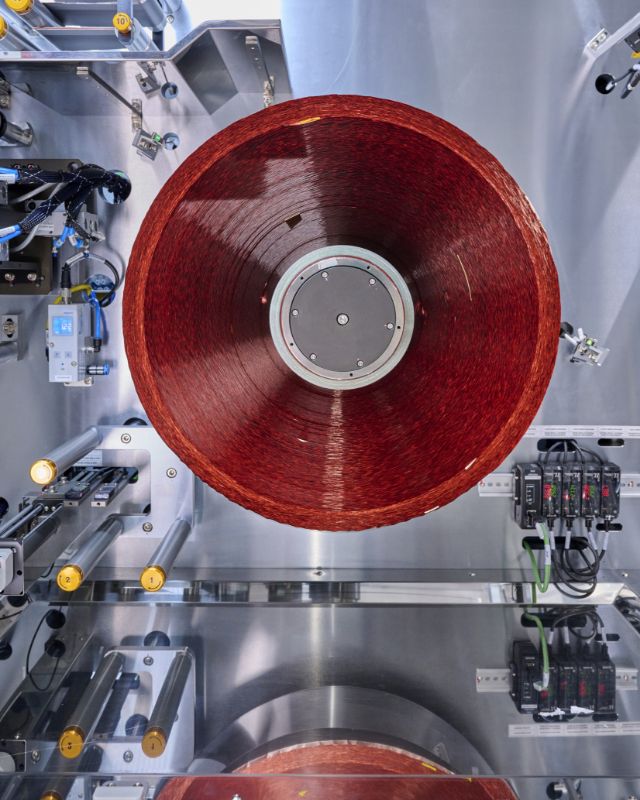
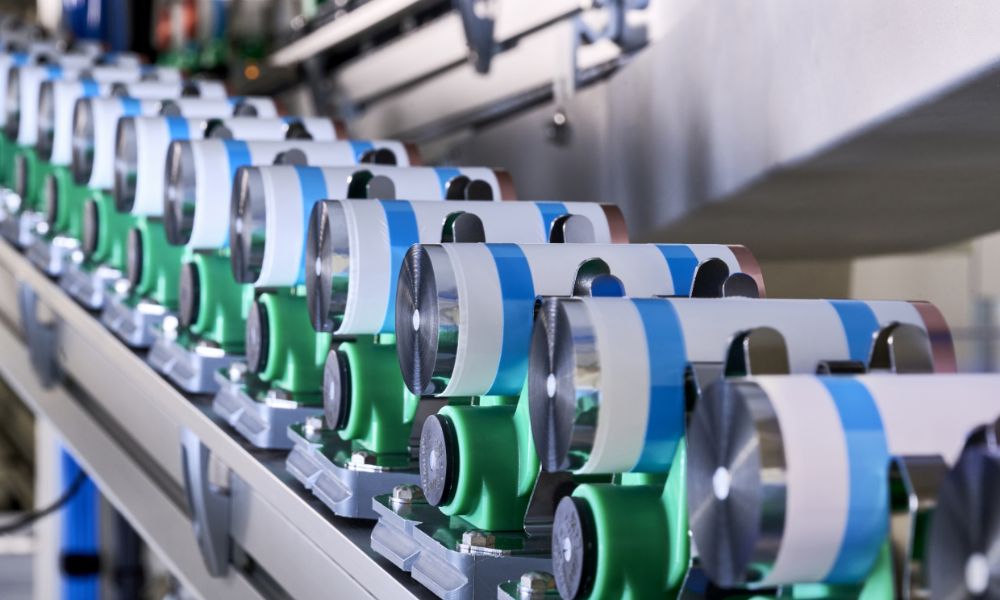
In der Zellmontage werden die beschichteten Folien, in der Fachsprache als kalandrierte Elektroden bezeichnet, mit dem Separator zu sogenannten Jelly Rolls gewickelt und in das Zellgehäuse eingesetzt. Die Zellen werden nun mit Elektrolyt befüllt.

Die Rundzellen werden zum ersten Mal geladen und abschließend überprüft.